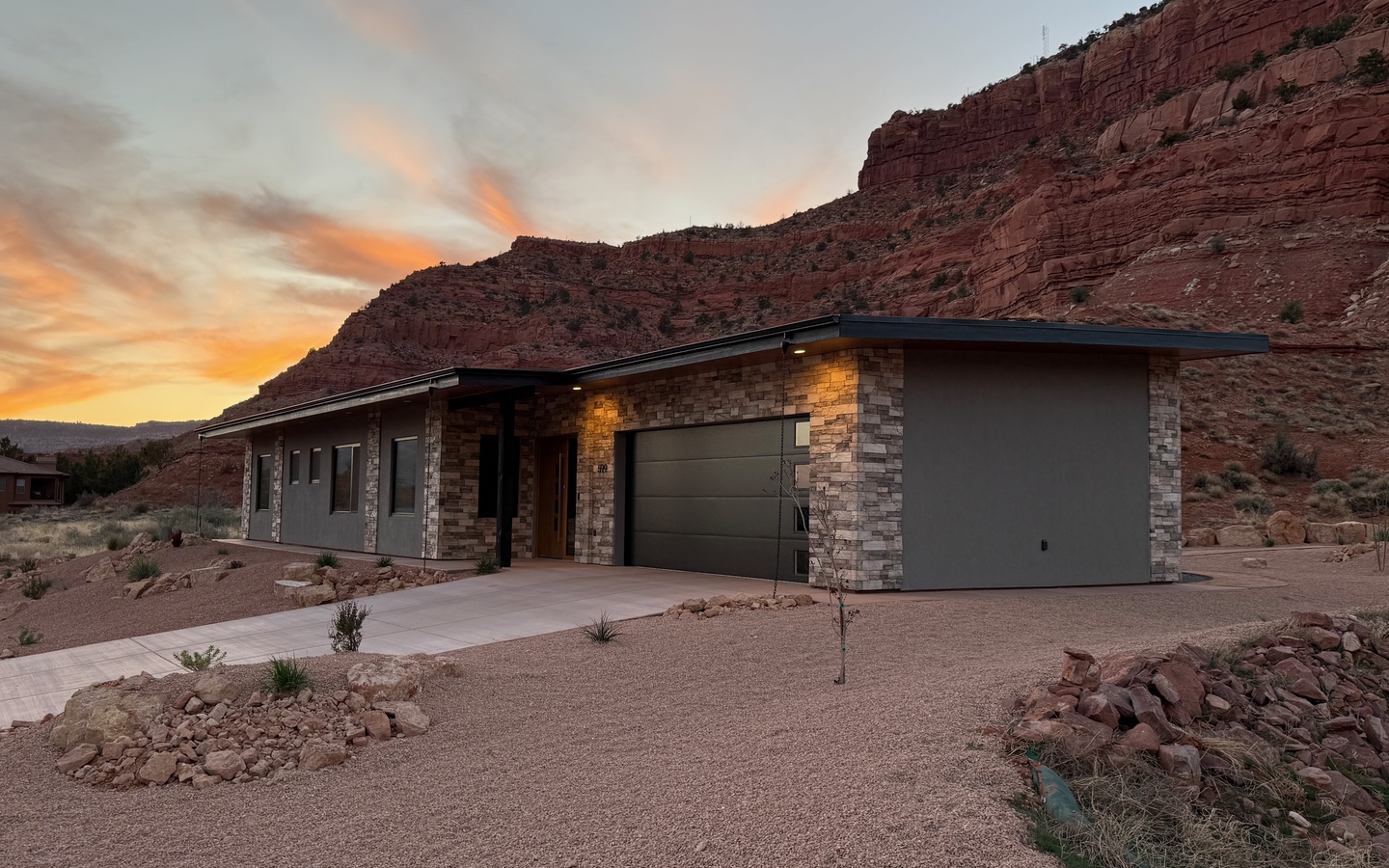
Photo Tour
Apr 12, 2025
Apr 12, 2025
Apr 1, 2025
Mar 4, 2025
Mar 1, 2025
Feb 15, 2025
Feb 3, 2025
Jan 13, 2025
Dec 21, 2024
Dec 8, 2024
Nov 25, 2024
Nov 12, 2024
Oct 31, 2024
Oct 24, 2024
Oct 23, 2024
Oct 6, 2024
Sep 1, 2024
Aug 21, 2024
Aug 4, 2024
Jul 30, 2024
Jul 28, 2024
Jul 25, 2024
Jul 17, 2024
Jul 17, 2024
Jul 4, 2024
Jun 18, 2024
May 30, 2024
May 17, 2024
May 5, 2024
Apr 19, 2024
Mar 30, 2024
Mar 28, 2024
Mar 26, 2024
Mar 13, 2024
Sep 11, 2023
Apr 11, 2023
Apr 2, 2023
Mar 28, 2023
Mar 25, 2023
Mar 20, 2023
Mar 17, 2023
Mar 15, 2023
Mar 13, 2023
Mar 12, 2023